The Hallock & McMillan building in downtown Portland is a vital piece of Oregon’s history. Built in 1857, it’s the oldest standing commercial building in Portland. It’s so old that Oregon wasn’t even Oregon when it was built – its statehood wasn’t established until 1859. Designed by Oregon’s first licensed architect, it was one of the first buildings in Portland to utilize cast iron in its masonry. Today, the average passerby would be clueless to Hallock & McMillan’s exceptional history. The building is now unassuming, its cast iron facade covered to comply with a more modern style. Its original design begs to be unmasked to regain the appreciation it deserves. A project of this kind is no small endeavor. It will take patience, meticulous planning, and expert design. Enter Emerick Architects.
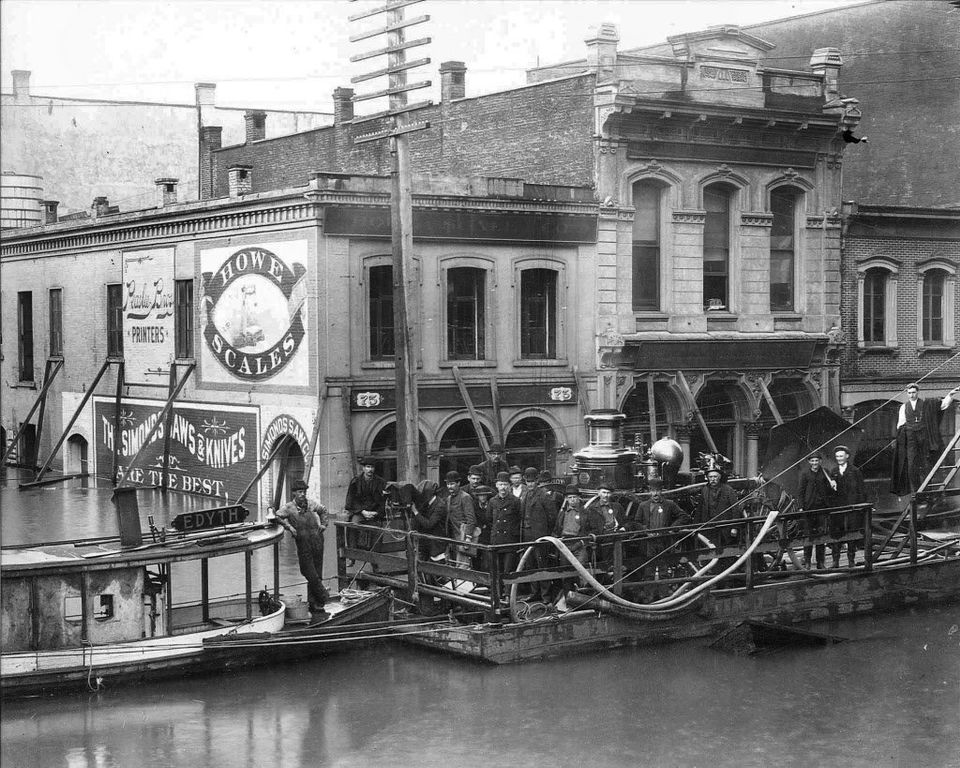
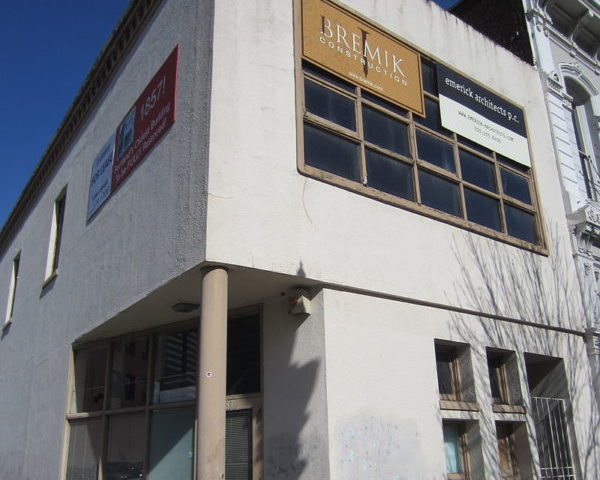
From left to right: Hallock & McMillan Building ca. 1894; modern-day Hallock & McMillan building
When the Emerick team began the Hallock & McMillan project, they knew the work would be extensive. It would require a team of experts to restore the building to its original glory, starting with the recreation of the cast iron facade. “This is a story about reconstructing a building’s face and place in history while staying true to its innovative past,” said Brian Emerick, Principal at Emerick Architects. Rebuilding the Hallock & McMillan building’s original facade is a painstaking but important process.
How do you recreate a historically accurate representation of an 1857 building in 2019? Using the same methods and materials from when it was built.
In order to create replicas of the cast iron pieces, the originals are removed from the building, sketched by hand, and made into carved wooden pieces by Architectural Castings. Architectural Castings specializes in history masonry reproductions, and is one of the few companies in the country that do so. Once they’ve produced the wood-carved replicas, they’re then pressed into sand, which hardens around the wood pieces to create moldings. The Silverton Foundry uses the moldings for the next step in the reconstruction process.
At The Silverton Foundry, furnaces are heated to a whopping 2800°F. Scrap metal is tossed into the furnace, creating hot liquid iron that’s then poured into the sand moldings. Once cooled, the moldings open to reveal exact replicas of the facade pieces. The process is time-consuming, but is a worthwhile cost for design accuracy.
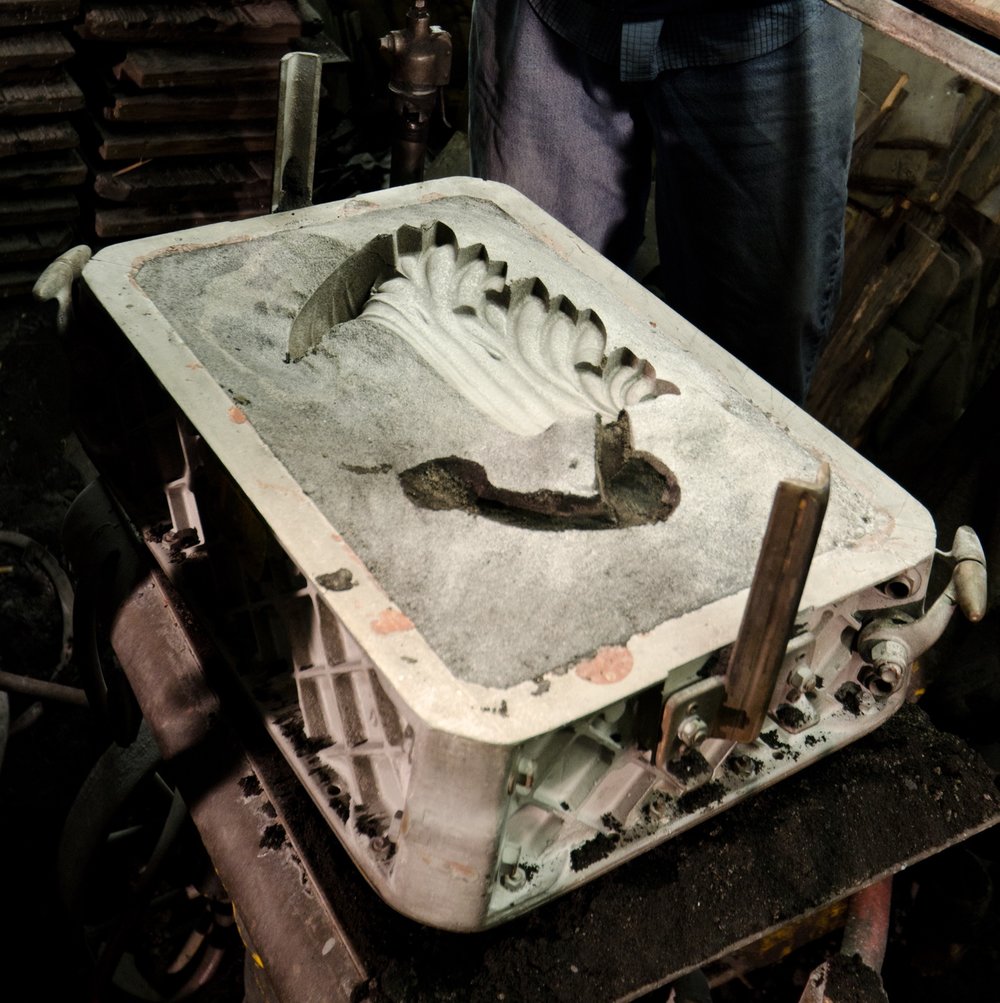
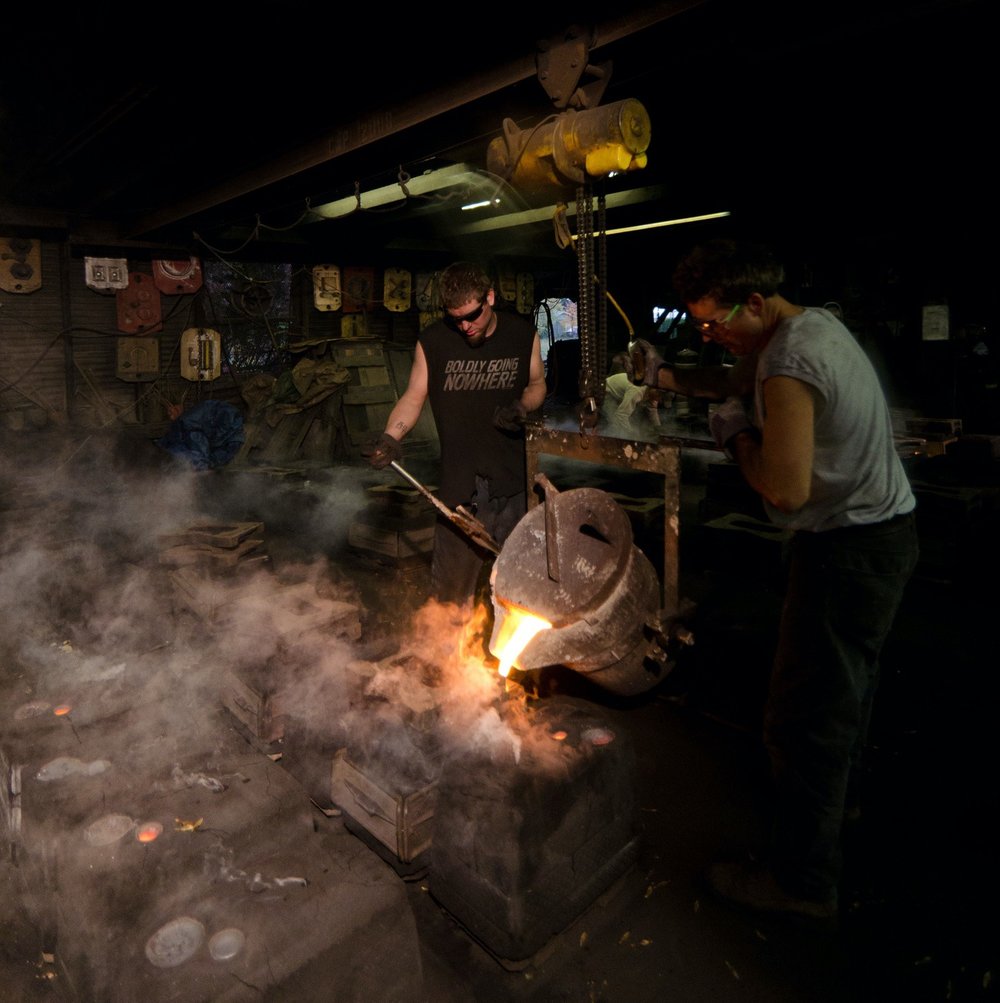
From left to right: sand-cast molding of facade piece; Silverton Foundry workers pour hot metal into molds.
The Hallock & McMillan building will eventually stand exactly as it did 162 years ago, but with improvements compliant to the 21st century. When it was first constructed, the building was considered a cutting-edge showcase of fireproof construction techniques. Today, a cutting-edge seismic upgrade is key to the building’s longevity. Emerick’s plans for seismic retrofitting include Hallock & McMillan’s neighboring buildings–all three will be safe in the event of an earthquake. Brian Emerick brings a wealth of knowledge on this subject as a member of the policy committee for unreinforced seismic retrofitting.
“When it’s complete, the seismic upgrade on the Hallock & McMillan building will not only ensure its survival after the big one, but also that of its historic neighbors,” said Brian. “It will be the lynchpin of a unique collective building seismic approach.”
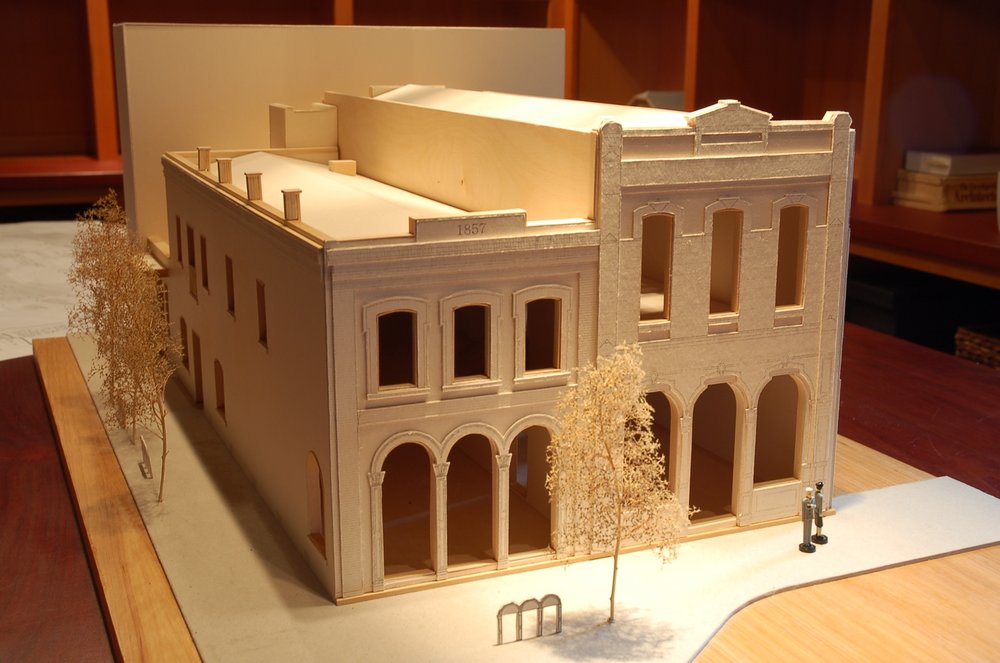
3-D model of Hallock & McMillan building
Reconstructing history is no easy task, but it’s a task not foreign to Emerick Architects. There is a shared passion for preservation with everyone involved in the Hallock & McMillan project. “The chance to restore the oldest commercial building in the city that predates Oregon’s statehood…it just has to be done and it has to be done right,” said Developer John Russell. “In its final state, it will be a magnificent building…exactly the way it looked when it was new.”